On a tour of the Gevorkyan factory in Vlkanova, Slovakia, a visitor may feel that they are at the centre of the most technologically advanced industry. The robotic presses never stop pressing powder, arms transfer parts, new products roll out of the 3D printer and technicians check for micron deviations on the computer. Artur Gevorkyan can not conceal his pride as he sees his factory working around the clock. “We are constantly pushing the boundaries and have absolute control over the entire process, right from the production of the material,” he says. He does not forget to add that although the factory is equipped with the most modern equipment, powder metallurgy is historically the oldest stage of processing metals and their alloys. Mankind has been familiar with it for more than five thousand years. The ancient Egyptians used it to make jewellery, which adorns Tutankhamun’s tomb to this day. The Incas or Greeks then turned the powder into weapons.
It wasn’t long before the powder literally meant money. “Powder metallurgy technology is about the only technology that was developed when money was being made. The gold, silver and copper powder was used to mint coins that were worth as much as the material itself,” says Artur Gevorkyan, adding that for such “large-scale production” one coin had to be the same as another. “We don’t manufacture money anymore, but the principle of our work is the same,” adds Armen.

“We are not an assembly company,” says Artur Gevorkyan, adding that his company’s goal is not to sell products, but to find solutions for clients. “We are a development supplier for most of our customers. The goal of our specialists, along with the customer’s developers, is to find a way to minimize the cost of our product and the overall assembly, such as the gearbox,” he adds, adding that the principle of powder metallurgy is not complicated to understand. As a rule, the mixtures are pressed or injected into moulds and then baked at very high temperatures.
Today, the company produces more than 5 million parts per month and launches more than 150 new products per year for clients in more than 30 countries. “But I am most proud of the 145 employees. It may not appear that way, but we’re not a company for normal people. Our colleagues have to live for their work and look all around and think about what could be produced by powder metallurgy,” he adds.

From Armenia via Ukraine to Central Slovakia
Artur Gevorkyan’s father was one of the founders of the powder metallurgy industry in Armenia, where Artur comes from. To this day, he sees Gevorkyan as more of a family business. The close ties are also evidenced by the fact that his son Robert works with more than a dozen other experts as a quality manager. “I’m trying to teach our people that we have to work together as a family, otherwise we have no chance to survive,” says the company’s founder.
Paradoxically, Artur himself did not originally want to pursue powder metallurgy. He studied aeronautical engineering at the military academy in Kharkiv, Ukraine. “I am an aircraft designer and I graduated from a military academy. When I decided to leave the army, I had to start learning something. Since I had been listening at home since I was a kid that powder metallurgy was great, I decided to go for it,” he says, describing the year 1991, when he founded a metallurgical enterprise in Ukraine. In 1996 he moved production to Slovakia, where he built a greenfield factory. “My goal back then was not to come to Slovakia, but to leave the former Soviet Union. Our whole business was and is based – and will remain so – on having neither suppliers nor customers in this part of the world and not being connected financially,” Gevorkyan told Seznam news.
We build on the more than 50 years of experience of two generations of our family.
Although Artur Gevorkyan considers Vlkanova, Slovakia, to be an ideal strategic location in the heart of Europe, the company is also establishing a development centre in Vienna, where it will move its R&D staff. “Powder metallurgy is not studied in Slovakia. Sweden, Spain and Austria are the closest. That’s why we have opened a development centre in Vienna, where we already have expert cooperation with universities,” Gevorkyan adds.
Truly waste-free production
The advantage of powder metallurgy is that almost no waste is generated during production, unlike conventional machining. If there are any small leftovers from the production, we can grind them up and reuse them. The entire production process is energy efficient, low-emission and saves raw materials. In addition, renewable energy is used in the production process. “In this sense, the technology is truly green and waste-free,” says Artur Gevorkyan. All furnaces are so-called amphibious and operate on gas as well as pure hydrogen and nitrogen. “As long as there is air on this planet, we can still produce,” he adds.
Artur Gevorkyan also considers it a competitive advantage that nowhere else in the world are all four key powder metallurgy technologies in one place. Currently Gevorkyan specializes not only in the automotive and oil industries but also in the production of compressors or in the security system, medical or fashion sectors The company’s customers include Linde, Komatsu and Siemens. The company also works with fashion brands such as Yves Saint Laurent and Versace, for which it produces metal clasps and decorations.

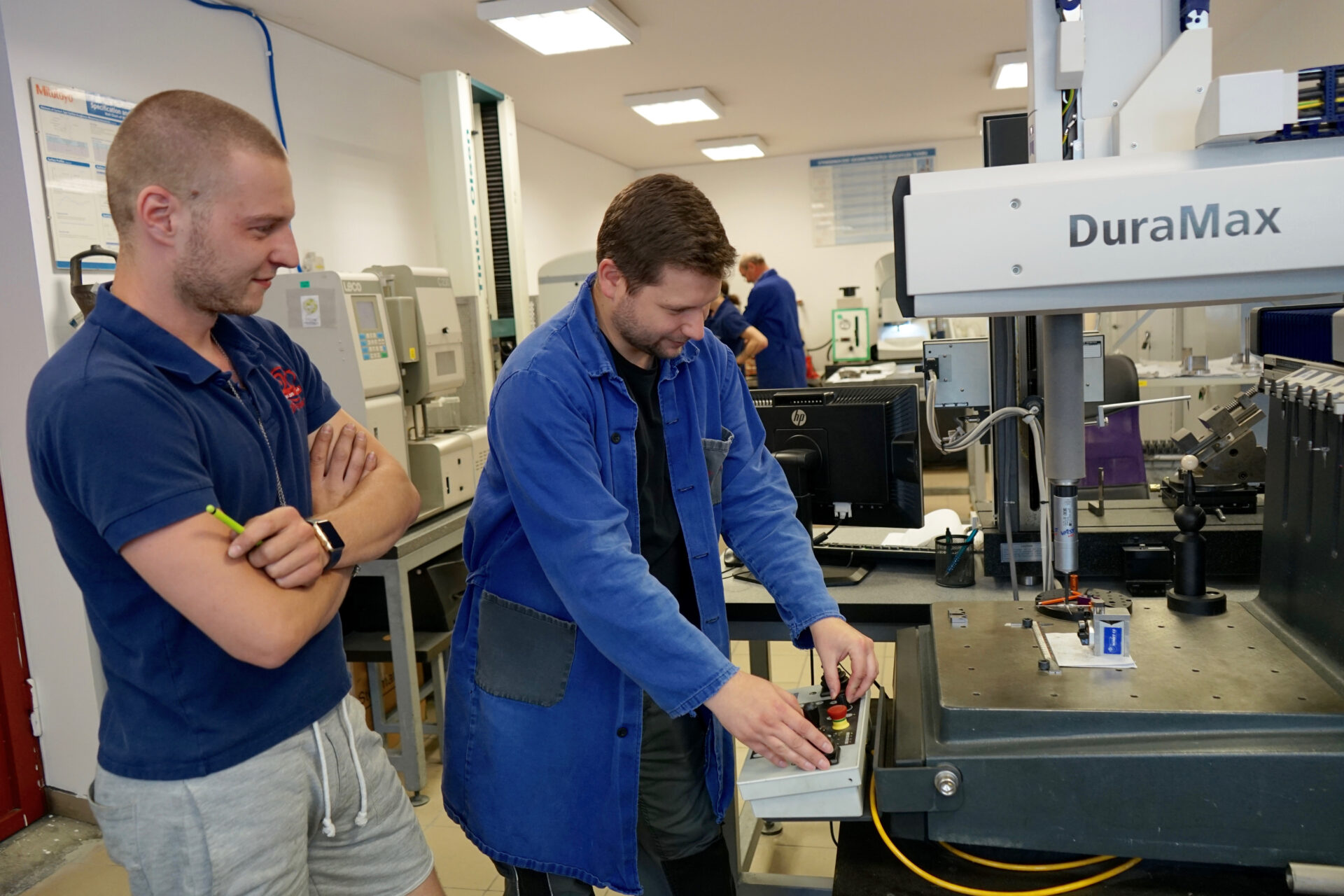
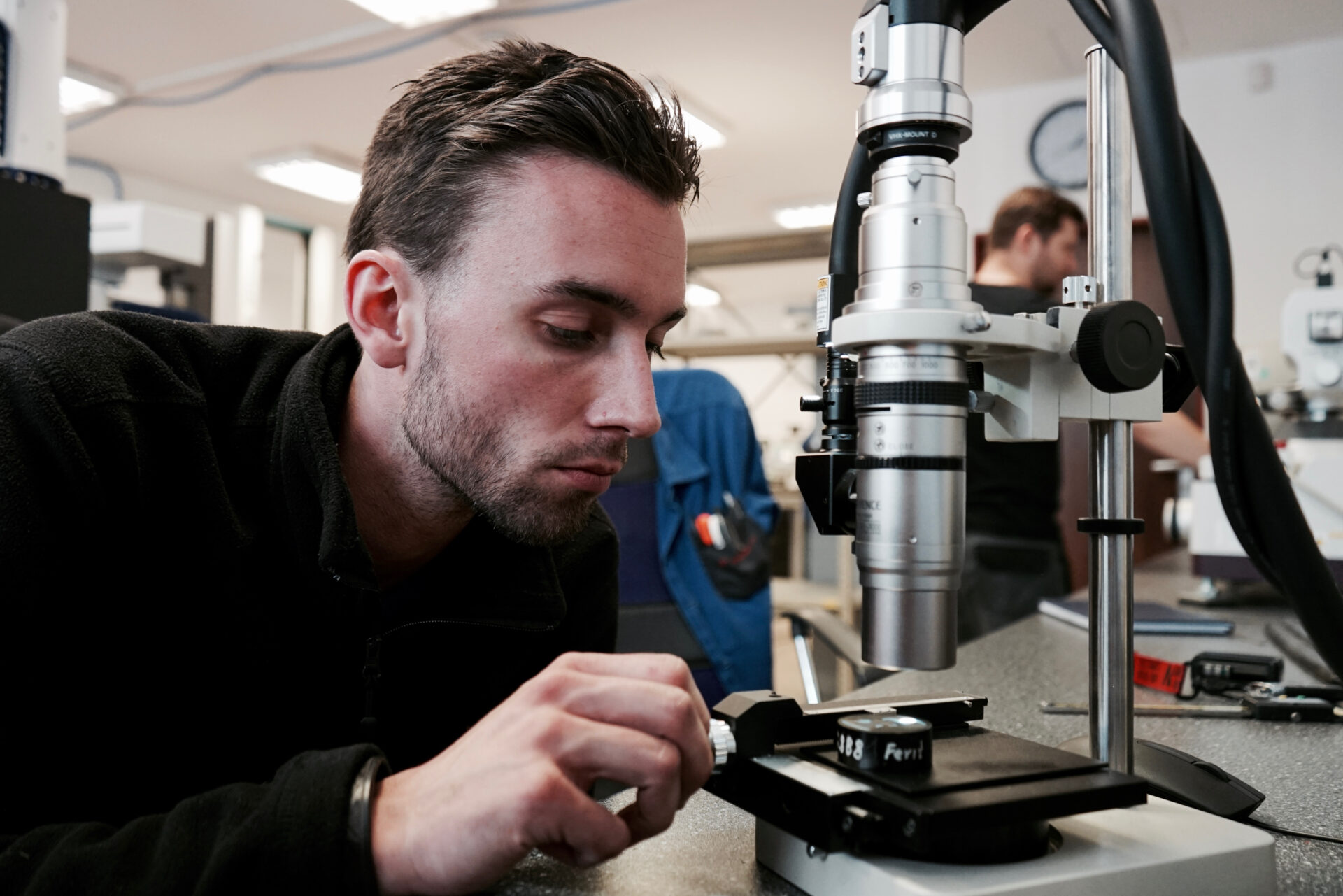

A company focused on stability
The Gevorkyan factory is different in many ways right from the front door. The walls of the offices are decorated with motivational posters that often refer to the Czech First Republic entrepreneur Tomáš Bat’a. “I admire Bat’a, I have his books by my bedside, but in one respect I am against him. Our customer is not our master, as he claimed. At Gevorkyan, the customer is our partner,” he says. In other respects, however, it adheres to the principles of Tomáš Bat’a. For example, each employee has a choice in the employment contract that the large manufacturer signs with its employees. For example, the principle that every employee should bring suggestions for improvement or that the company does not want to cooperate with those who plan to stay with manual work. “A hundred years ago, Bat’a talked about what we now call Industry 4.0,” adds the businessman.
Artur Gevorkyan also admits that he is not one of those entrepreneurs who are driven forward only by the vision of success. “I didn’t need to prove anything in particular in my life. Sometimes I just wanted to survive. I know what it’s like to eat off one plate with my wife. I know what it’s like not to have money,” he recalls. This is why he places enormous emphasis on stability and diversification of production into different sectors of the world economy. “During the pandemic, the automotive industry went down, but the demand for hand tools increased,” he says.
-
Since 2010, Gevorkyan has increased its revenues from €4.7 million to more than €48 million in 2020 and more than €53 million in 2021.
-
The company’s gross EBITDA operating profit in 2020 will reach € 12.5 million (approx. CZK 330 million) with an EBITDA margin of approximately 26 percent. In 2021, the gross operating profit reached € 16 million which indicated the EBITDA margin of appx 30%.
-
Net profit in 2020 reached €3.7 million, a 40 percent year-on-year change compared to 2019. For 2021, the net profit is provisionally EUR 4 million.
Billion-dollar development with the Start market
Artur Gevorkyan sees the entry into the Start market as another step in approaching the future of his industry and a new stage in the company’s development. So far, innovation has been financed in several forms, from loans to bonds to private equity. Artur Gevorkyan emphasizes that his company has always regularly met its planned indicators and fulfilled its commitments. “We consider the issue to be the next logical step in our vision and goal to build a business with revenues of EUR 300 million or more. We plan to list our shares on the main market of the Prague Stock Exchange within five years,” says Artur Gevorkyan.
The company currently plans to use the money from investors mainly to expand production and purchase factory robots. “I see so many projects and years and years of work ahead of us now, and I’m held back by one thing: I’m not keeping up with capacity. We have two meetings a week on this – who to prioritise and how to resolve it. And this has been going on for years,” adds Artur Gevorkyan. Therefore, the company has already purchased land within the existing site to meet demand.
According to Artur Gevorkyan, the new stage will involve not only him but also his entire team of more than 100 people. And they are not afraid that this will potentially be the largest share subscription on the Start market. Indeed, like it says above the front door of the factory in Vlkanova: “We behave like a family. We fight like an army.”